Mini-Sextant Tracking Mount
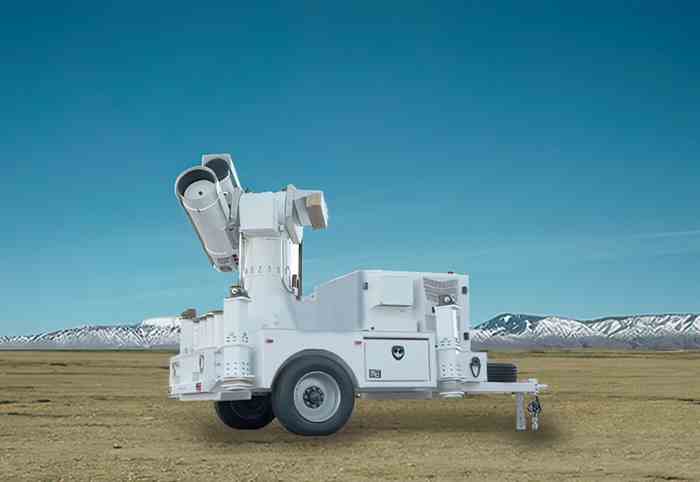
Mini-Sextant Tracking Mount
Introduction:
The Mini-Sextant provides four sensor stations for collection of highly accurate Time-Space-Position-Information (TSPI) or engineering Sequential Data (ESD) from high dynamic airborne targets. The Mini-Sextant has a significant amount of torque in azimuth and elevation and will provide dynamic performance equal to that of the MMTS. Its unique balance of available torque, positioning accuracies and payload flexibility allows the system to be configured with optics best suited for close-in launch missions or down range for longer range fly-out missions without compromising dynamic performance or accuracy.
Payload Flexibility:
Photo-Sonics has over 50 years experience in the design selection, fabrication and integration of sensor suites on Optical Tracking Systems (OTS). Depending upon your mission needs, a fully integrated Mini-Sextant can be configured with a combination of long-range / short-range optics with a combination of long-range / short-range optics, and laser range finders. While the recommended maximum total payload is 181.4 Kg (400 lbs), additional payload may be supported with reduced dynamics and accuracies.
Robust Pedestal Construction:
Photo-Sonics utilizes Almag‑35, an aluminium magnesium alloy, which provides excellent corrosion resistance to support long life with minimal maintenance in the harshest environments. We use only full size bearings to provide the highest stability and accuracies, as opposed to narrow diameter bearings found in lesser systems. Powerful, DC torque motors are provided in both the azimuth and elevation axis are coupled to the identical 9-inch diameter, 24-bit optical encoders used in our flagship tracking system, the MMTS.
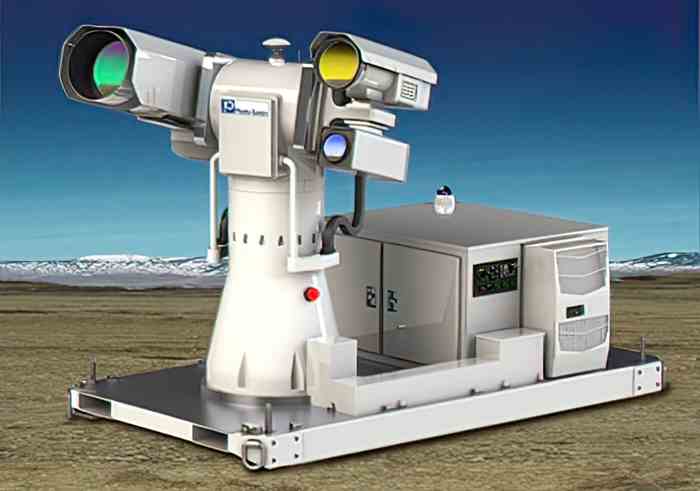
Mini-Sextant: Palette Mounted

Mini-Sextant: Pedestal Mounted
Pedestal Support Electronics:
The modularity of the Mini-Sextant control electronics supports several installation scenarios. The Trunnion Computer Unit, vital for real-time operations of the pedestal, sensors and optics is located within the pedestal. The Digital Servo Amplifier (DSA), RFI power filters and I/O panel are packaged in enclosures at the pedestal site. The remaining electronics such as Base Computer Unit (BCU), Video Switches, Video Trackers, Video Recorders, etc., are installed in the Operator's Console which can be located in a mobile Operations Van or at the user’s Mission Operation Centre.
Control Software:
The ARGUS control software provides all the functionality the user would expect of an advanced TSPI tracking system. It provides a single interface for the tracking pedestal, sensors, auto-tracking, radar, calibration, target simulation and diagnostics of the complete tracking system. Control of the system is simplified via an intuitive touch screen GUI. The standard ARGUS application can control up to 10 sensor stations, in addition to radar and lasers, allowing a single-operator complete control of all aspects of a complex and highly capable system from a remote location. It also provides the control of single and dual-gate auto trackers and fixed focal length and zoom lenses and focus tables. Automated Star calibration are incorporated to yield the highest TSPI accuracy of any optical tracking system manufactured today.
Operator Console:
Photo-Sonics offers a variety of console configurations, from our full- size console (for location in mission control centre) to smaller, compact consoles suitable for mobile command vehicles or multiple packing cases for transportability. The default connection between the pedestal and the remote console is via a single-strand, single-mode 'dark' fibre optic cable, which allows for up to 20 km separation. Alternative interfaces including shared fibre optics and microwave are also supported.
Key Specifications:
System Accuracy, Fixed Mount | ±10 arc-seconds (50 micro-radians), 2σ |
Bearings | 711.2 mm (28”) diameter azimuth thrust bearing 406.4 mm (16”) diameter elevation ball bearing |
Drive System | Direct drive DC torque motors (brush type) |
Torque | Azimuth: 475 newton-meters (350 foot pounds) Elevation: 475 newton-meters (350 foot pounds) |
Velocity (nominal payload) | Azimuth: 120°/second Elevation: 120°/second |
Acceleration (nominal payload) | Azimuth: 120°/second² Elevation: 120°/second² |
Closed Loop Servo Bandwidth | Azimuth: 8-10 Hertz (payload dependent) Elevation: 8-10 Hertz (payload dependent) |
Nominal Payload | 200 pounds per platform (at rated payload moment of inertia design specification) |
Non-Orthogonality | ± 5 arc seconds |
Encoders (optical, absolute) | 24-bit |
Elevation Travel | -15° to +195° |
Azimuth Travel | ±270° (cable wrap configuration) Continuous (slip-ring configuration) |
Transit Locks | Locking stow pins in azimuth and elevation axis |
Height | 1981.2 mm (78”) (pedestal base) |
Power | 3-phase European or US AC power |
Note, all specification subject to change
Configuration and System Options:
A standard console consists of the following items ...
- 19" Touch-Screen Monitor for the main GUI interface
- Video Monitors (2, 3, or 4 screens available)
- Operator Control Panel
- Mini Keyboard with Control Stick and Operator Controls
- Console Computer
- I/O Panel (Fibre optics, Ethernet switches)
- Optional UPS
Optical Tracking Systems Product Menu : Close-In - Mini-Sextant - Fly-Out
For more technical details, contact a member of the team at Photo-Sonics International Ltd.